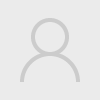
Quser(UID:157115) 新手上路
主页访问 : 2606 次
发问
没有内容
回复
方法应该有很多种种,可以从流程动作漏洞角度从人的方面下手,为什么人会漏检,互检机制失效起分析,也可从防呆角度,在此工序后加个光学自动检查,用工业摄像头来自动检查,不依靠人靠防呆.
2012-07-13 13:19
循序渐进.叫什么名字并不关键,关键是它的管理体制和人员品质意识能否满足这个要求.
2012-08-03 16:44
这两者相差可大啦,VSM侧重整体改善,宏观可到整个供应链,微观可到至单个产品的具体一段流程,而线平衡改善仅是现场改善的工具之一,适用范围不是一个数量级的.
2012-07-13 13:24
正在找的资料,比较下与在用MTM法有何异同
2011-06-01 16:56
关键是理解精准思想的精髓,切实掌握其应用和实践经验,用张小纸片很难衡量的,至于考试和认证,公众认可度又多高呢,要三思而后行。
2011-05-11 14:42
企业要有生存的压力,高级管理人员要有很强的忧患意识
2011-01-07 11:25
生死存亡之际,所示方法均不管用,请个高人做下企业诊断,或老板自己搞个短期决策吧,生存是头等大事
2010-09-21 14:43
HEIJUNK 就是要通过均衡化订单,减少最小生产运行批量,平衡订单的波动,对于多品种小批量的情况最为适用.如订单较大且相差不大种类,可直接用流水线,没必要强制用HEIJUNK混流生产.
2010-09-21 13:29
应该要设的,超市.如果你的产品工序较多,可以先分一下产品族按流程
2010-09-21 14:29
长期方案,改进设计,尽量统一螺丝的种类和数量,避免相近的螺丝使用在易混的工位上.短期方案如楼上有的兄弟所言,使用计数电批,避免装漏或多装.再者可以试下调整工位布局, 如果还搞不定,发动一线操作员工搞个QCC圈活动重点搞下.方法总比问题多!
2010-09-21 14:40
两点建议,1)U形布局设备,方便产品族混线生产 2)推行QCO,快速换模
2010-09-24 09:36
首先该检验能否去掉,能不做最好不做,如果必须须做,检验的时间可以当做一个工序来处理,至于具体的时间应参照标准时间计算方法
2010-06-15 11:31
of course LP,but not familar "NPS",how come?
2010-06-15 11:45
IT电子组装,插件,机械组装,应该坐着好些. 必竟对于这些轻工装配来讲,坐着更有利于员工稳定品质,员工疲劳强度更低些, 不赞同小日本的针对这些的站立作业
2010-06-15 11:42
楼主所用的无法真正的靠,不能在舒缓作业员疲劳
2010-06-15 11:44
楼主所用的无法真正的靠,不能在舒缓作业员疲劳
2010-06-15 11:44
这涉及到MCT如何计算的问题,MCT并非每件产品时间的简单相加. VA & NVA的计算最主要的是计算WORK CONTENT %,这是衡量LEAN PROCESS 的一个重要指标,可以借此发现如何降低INVENTORY 和MCT,这个意义就大了,希望我讲明...
2010-04-27 18:38
首先从工装设计,W/S调校,相关设备,二者可以兼容,把SMED嵌入到拉设计中去,2PCB放置方向交叉易于作业员区别,当然最重要的有多能的作业员
2010-04-14 11:27
GEMBA日语原意是现场的意思,GEMBA FIRST,到现场去发现问题解决问题,这是大野耐一的一贯主张.坐办公室时永远得不到第一手准确情报,发现不到真正问题
2010-04-21 11:19
每个公司也不一样,没有硬性统一要求,只要公司内部统一就可以 具体情况具体分析
2010-04-27 18:42
IE的范畴要大一些,LEAN可看作其一个分支.当然LEAN 有的涉及面也比较宽,有些交叉性. IE源自USA,LEAN 则源自小日本丰田.
2009-11-18 18:37
看来一贯是LEAN标杆和鼻祖的丰田也在库存上载了跟头,无语!
2009-11-18 18:39
Tack time的計算公式是 TT=working minutes per day/line rate, line rate=customer expected deman/during working days
2009-10-29 15:06
考虑左右手操作习惯是个主要方面,正如楼主所指.问题是关键是参照具体情况而定,不一定墨守成规.这个问题业内是有争议的,我曾专门跟公司一位精益大师探讨过,他的观点也基本是这样的
2009-10-29 12:26
做过几个案例,感触颇多.VSM是个好东东,从全局出发,不在局限于一点.关键在于所处的层次高了很多
2009-10-29 12:29
好文章,不在意其数据是否经得意推敲. 推行CELL LINE好处多,当然也困难重重,搞定后成就感有一点. CELL line 与流水线各有适用处,不可一概而论.我朋友的公司老板就硬把一条流水线必成CELL,结果惨不能忍睹
2010-04-09 10:02
文章
没有内容
最新动态
2013-07-12 Quser 回答了问题:
2013-07-12 Quser 回答了问题:
2013-07-12 Quser 回答了问题:
2013-07-12 Quser 回答了问题:
2013-07-12 Quser 回答了问题:
2013-07-12 Quser 回答了问题:
2013-07-12 Quser 回答了问题:
2013-07-12 Quser 回答了问题:
2013-07-12 Quser 回答了问题:
2013-07-12 Quser 回答了问题:
2013-07-12 Quser 回答了问题:
2013-07-12 Quser 回答了问题:
2013-07-12 Quser 回答了问题:
2013-07-12 Quser 回答了问题:
2013-07-12 Quser 回答了问题:
2013-07-12 Quser 回答了问题:
2013-07-12 Quser 回答了问题:
2013-07-12 Quser 回答了问题:
2013-07-12 Quser 回答了问题:
2013-07-12 Quser 回答了问题:
2013-07-12 Quser 回答了问题:
2013-07-12 Quser 回答了问题:
2013-07-12 Quser 回答了问题:
2013-07-12 Quser 回答了问题:
2013-07-12 Quser 回答了问题:
2013-07-12 Quser 回答了问题:
详细资料
- 个人成就:
- 最后活跃:
- 2016-07-22 18:20
- 登录次数:
- 16 次
- 注册时间:
- 2007-03-20 10:37